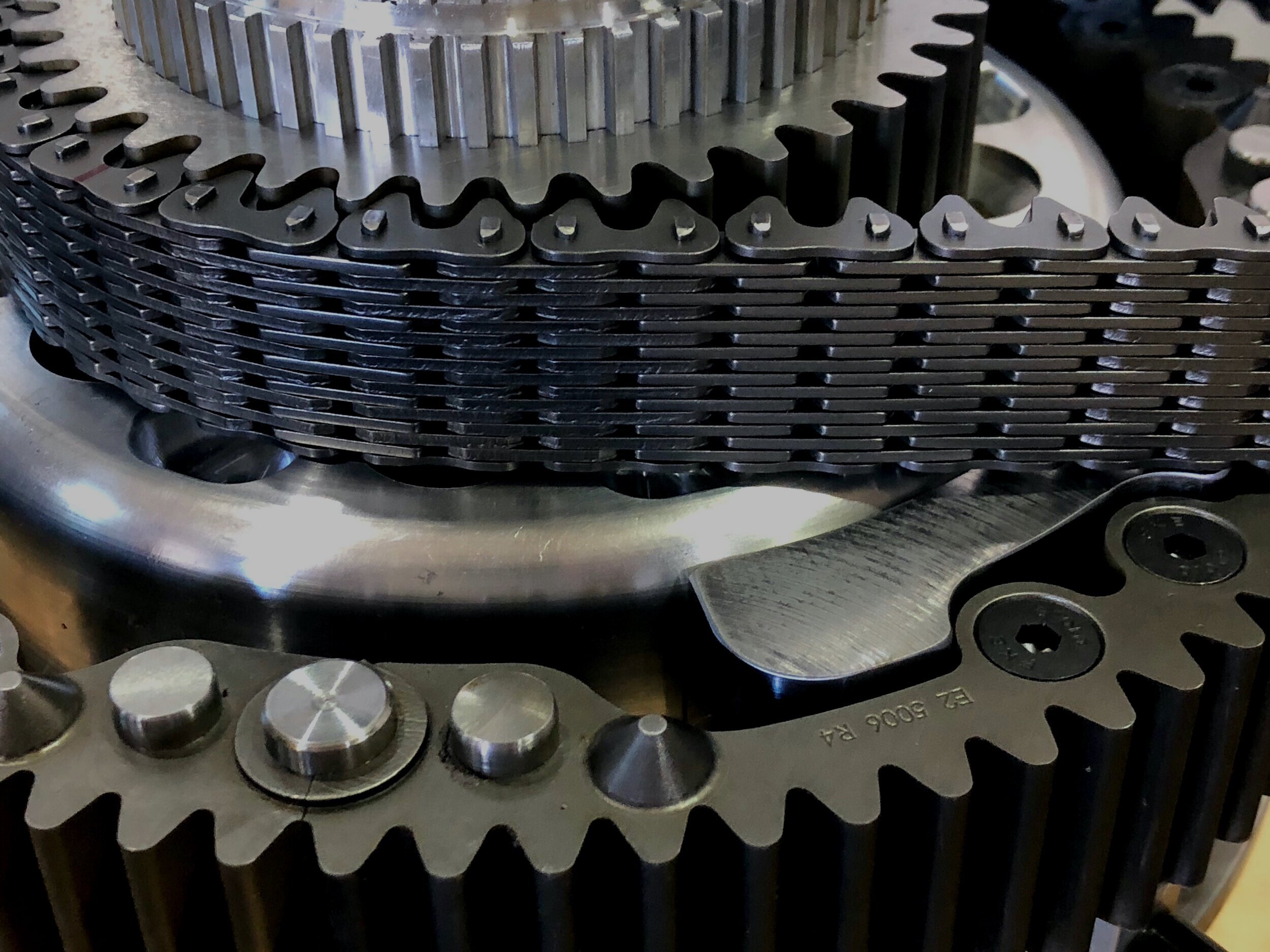
Ingear Technology
The Ultimate Transmission for electric vehicles: low-cost, smooth, quiet and extremely efficient
How It Works
Most EV motors in the market today are single-speed. Typically, there are two helical reduction gears between the motor and the wheels. The motor turns about nine times for each revolution of the wheels.
Ingear replaces the second reduction gear with a continuous chain drive and an innovative morphing sprocket that resizes during a shift. The entire shift happens during a single revolution of the wheels.
To shift, an actuator directs outer gear segments in or out of the chain path, while the motor speed is carefully adjusted so that shifts are barely perceptible and can be completed in as little as 19 milliseconds.
Combined with a chain and chain-tensioner, Ingear provides for 2:1 or similar gearing ratios. The extremely efficient chain is always kept in line with the morphing sprocket.
Low-gear is used to move the car from a standing start to half of highway speed. High-gear is used for higher-speed driving. By enabling the electric motor to operate more efficiently, more of the battery’s power is used to move the car, and less is wasted as motor and transmission heat. Less waste means more range from each charge.
Continuous Torque Geometry
Ingear’s patented geometry keeps the motor in continuous connection with the wheels. Torque from the motor continues to flow to the wheels, even during shifting while torque fill algorithims maintain a smooth passenger experience. Similarly, regeneration is continuous, even while downshifting.
How is Ingear Different?
Comparing the Ingear to AMTs, DCTs, and CVTs:
Ingear has no clutch.
Ingear does not require a high pressure pump.
Ingear uses ball bearings instead of roller bearings as it does not generate axial loading from chain/sprocket meshing.
Ingear has no losses from multiple gear pairs engaged simultaneously, nor rolling contact losses.
Ingear does not generate heat due to losses or clutch friction, or rolling contact friction, so motor thermal rise is mitigated without introducing any load on the cooling system.
Ingear offers uninterrupted torque transfer during the shift.
Ingear has consistent/repeatable shifts by design. Other systems require closed loop control that adapts to wear and clutch performance.
Ingear only moves segments axially when they are not contacted by the chain. Actuator force is low. DCTs and CVTs require tens of thousands of newtons of force to shift because the actuators must modulate the traction motor force to the wheels.